Kingsford Sizzles with Sustainable Manufacturing
By Steve Clarke, Environment & Sustainability Group Manager
When you think about Kingsford, you probably think of cookouts, tailgating, great barbeque and high quality briquets.
One thing you may not know about is Kingsford‘s commitment to sustainable manufacturing.
“Each of our Kingsford plants has specific environmental and sustainability goals they’re working toward”, says Heath Rigsby, general manager – Kingsford. “We believe our plants are leading the industry in many sustainable practices, such as water reduction, sustainable sourcing and energy reduction.”
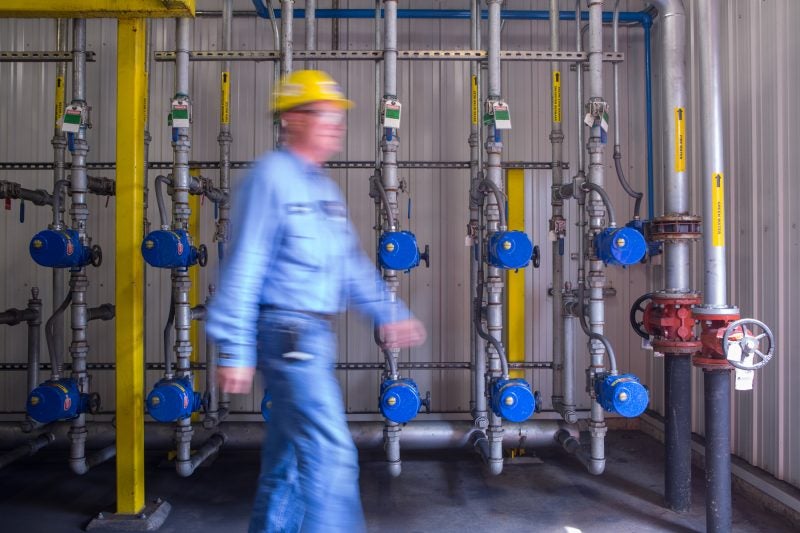
Safety is a core Clorox value. A Kingsford plant in Belle, MIssouri.
Building on a legacy of sustainability
This commitment to sustainable business practices actually dates back to the brand’s founding in the 1920’s, when Henry Ford decided to use wood scrap from his auto manufacturing processes to make charcoal briquets. Those first plants were models of sustainability, producing over 600 lbs. of briquets for every ton of scrap wood.
Today, our plants continue that same ethic, making charcoal briquets from natural products and wood waste generated by the forestry and lumber industry. “In fact, we’ve gone one better and can now produce 1,300 lbs. of briquets from every ton of wood waste”, says Clark Fisher, Kingsford senior engineer.
Another of our sustainable practices lies in how we manage production waste — the wood and char particles that fall to the ground as we make our briquets. The water we use to clean our plants drains into settling basins, from which we capture, remove and dry fine particles. The settling basins prevent the “fines” from getting into the storm water discharge, a significant environmental benefit. We then reintroduce these fines back into the briquet manufacturing process where they provide an added benefit: helping your charcoal light faster.
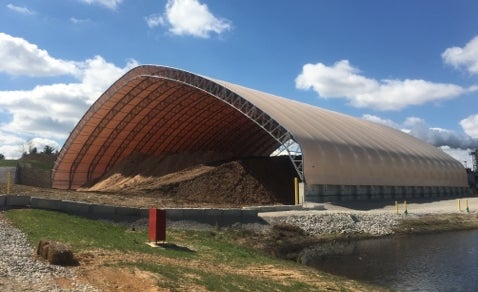
A woodpile cover at the Kingsford plant in Summer Shade, Kentucky, improves plant energy use by keeping raw materials dry.
To the last drop
The Kingsford plants also take pride in their water recycling programs. Much of the water used for quenching, dust control, wash-down and other processes flows into onsite basins or ponds to be pumped back to the plant for reuse.
“Most of our plants have dedicated water recycling systems, and the vast majority of the water used within the plant comes from the recirculation ponds,” says Michael Powell, environmental manager. “The creeks and streams around our facilities have healthy aquatic populations, and we take extra care to protect them.”
These water recycling systems have contributed to Clorox achieving its 2020 goal to reduce its water footprint by 20% from 2011 levels.
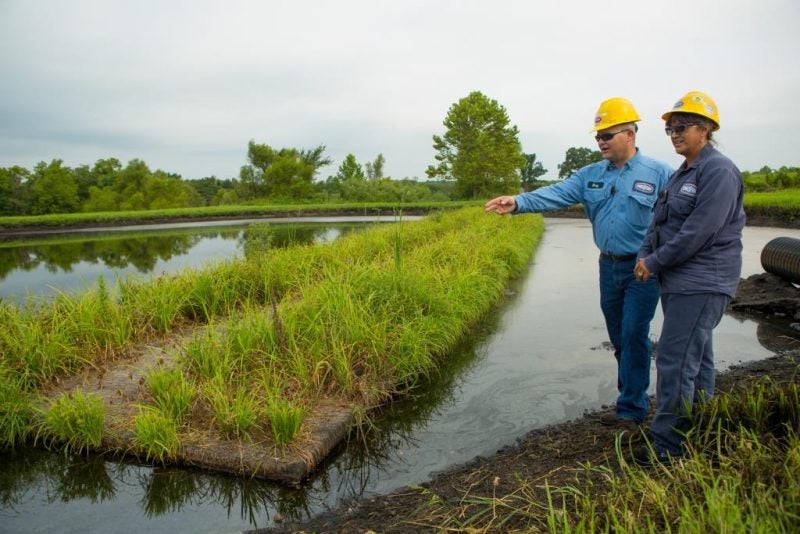
A man-made island in one of the water recycling ponds at the Kingsford plant in Belle, Missouri, helps filter the water.
And beyond, to natural gas and solid waste
Kingsford is also committed to sustainability in managing natural gas.
The plants use natural gas to start the process that turns wood into char, the main ingredient in charcoal. Once started, the combustion process becomes self-sustaining, reducing the amount of natural gas the plants use. The char and char fines are mixed with lime (which whitens the ash) and starch (a binder) and is compressed into briquets. Some of the waste heat from the charring process is used to dry the briquets before they are packaged. Waste heat is also used to preheat plant boilers. This allows the Kingsford plants to improve their energy efficiency.
Lastly, each Kingsford plant has been working hard to reduce the amount of waste it generates. In addition to recycling cardboard and plastic, several of the plants have initiated beneficial reuse projects for old concrete and used oven brick, which needs to be replaced every few years.
For example, the Summer Shade, Kentucky, plant used the inert brick as a base for an onsite road. The Belle plant had a project that involved regrinding old concrete and using it as a base for new pavement outside their warehouse.
“Each demolition project can generate several tons of waste that would typically be sent to landfills,” says Clark Fisher. “It’ a benefit to the environment whenever we can use some of this material on site.”
These are just a few ways that Kingsford works to minimize our impact to the environment.
“Whenever I visit the plants, I’m always so impressed by each one’s genuine commitment to sustainable practices,” says Heath. “This is a story we don’t tell enough, which is a shame because it’s one that should make us all very proud.”
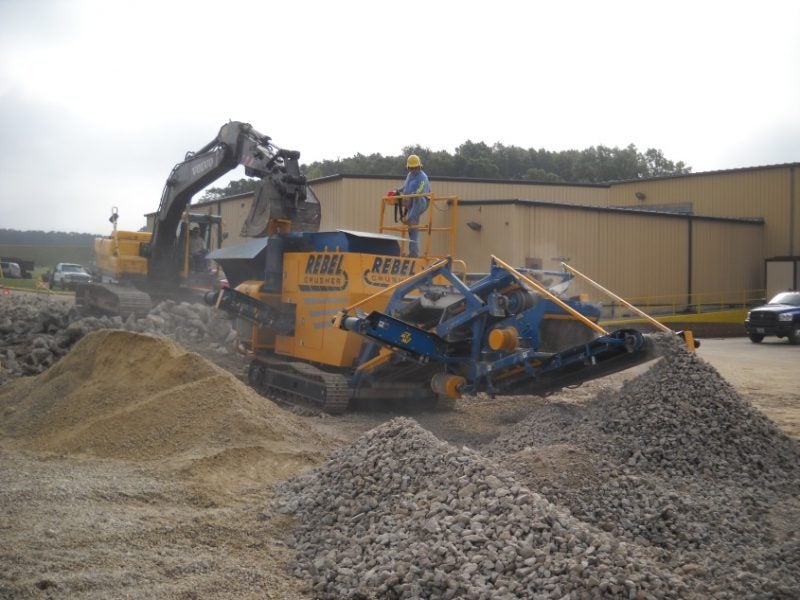
A capital project to expand a concrete area in front of a warehouse generated lots of old pavement, which the Belle, Missouri, plant crushed and recycled into sub-base.