Workplace Safety Is a Journey, Not a Destination
By Annette Cleaver, Corporate Safety & Health Manager for North American Manufacturing
Ever wonder what it takes to maintain a world-class safety record?
At The Clorox Company, we take safety very seriously. It’s a key component of our business culture, something we talk about daily. We’re proud of our world-class recordable incident rate (RIR) of 0.54 in calendar year 2015, and of how many of our sites have logged weeks, months, and in some cases even years, injury-free. These are hard-won achievements.
Still, a focus strictly on outcomes glosses over the behind-the-scenes work and daily commitment that go into a stellar safety record. Nor does it recognize those sites that may have injuries, but do an abundance of great work to keep those numbers to a minimum.
That’s why we’re starting to shift the conversation at Clorox away from numbers and outcomes to the efforts behind them. While we’ll always report the numbers — they’re both important and required, we feel a proper discussion of safety must be more holistic. It should focus on the safety process and reinforce the daily commitment that true workplace safety demands.
So here are some examples of how the people at The Clorox Company invest daily in safety and of the behaviors we value.
- The safety leader at each Clorox site aligns with local leadership and overall business needs to develop site-specific plans to advance safety and health.
- Site safety leaders and safety committees work together with local employees to manage current procedures, training, area audits, safety observations and safety improvements. They also get creative with “Safety Blitzes” — exercises that can focus on anything from improvements to machine guarding to housekeeping to chemical storage, handling and use.
- Cross-functional teams (think a mix of employees from R&D, Engineering, Manufacturing and Safety & Environmental, for example) confer regularly to identify potential issues early, before problems arise.
- Office safety teams emphasize the importance of good ergonomics, offering online training and a work station self-evaluation process, then providing additional support for those who need it.
- Providing networking opportunities for Safety Leads or Safety Pillar Team members to share best practices and ideas through monthly conference calls, peer safety audits and a biennial Safety & Environmental Conference.
- Piloting new ideas to support our 2020 Vision and growth culture. For example, our plants in Springfield, Oregon, and Burnside, Kentucky, have started Human & Organization Performance, a process to gain a greater understanding of the complexity of our work with the aim of understanding daily variability and what our employees must do to adapt to meet the production, safety and quality requirements.
- Taking a new acquisition that had very weak safety systems or processes, sharing Clorox’s value on injury prevention, providing a basic framework to improve and then seeing how quickly positive safety results followed. We saw this happen with the Burt’s Bees and HealthLink acquisitions.
- It’s accepting that even at sites that have been part of our company for years and are well entrenched in our safety culture, injuries can occur. It’s in knowing the most important thing is providing appropriate care for the individual employee. Once that’s done, we regroup and learn from what happened so we may gain a greater understanding and improve.
We believe that focusing on our safety effort rather than our safety record is a more powerful way to drive a culture of safety at Clorox. We’re committed to remaining world-class in this regard at all our sites, whether plant or distribution center, office or R&D facility.
After all, people tell the best stories, not numbers.
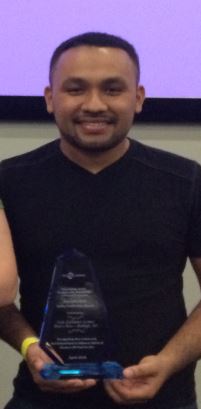
Luis, an employee at the Burt’s Bees plant, was recognized for his commitment to safety.