Our first food plant becomes zero waste to landfill
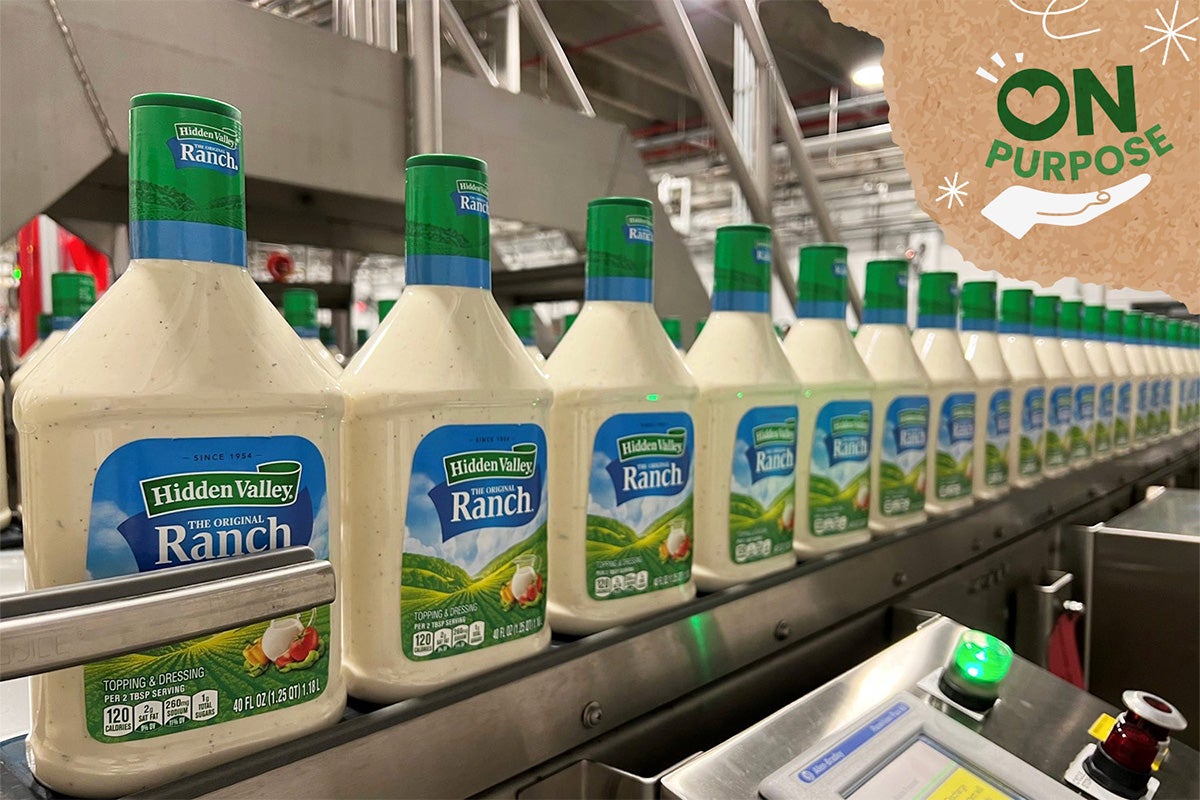
Clorox’s environmental, social and governance goals are integrated into our IGNITE strategy because we believe they create value for our company, brands, people and communities. We’ve focused on areas where we can make the biggest impact, and much of our progress is realized through the work of our purpose-driven brands.
Our Hidden Valley Ranch manufacturing plant in Wheeling, Illinois, recently became the first facility within our Foods business unit to achieve zero-waste-to-landfill, or ZWtL, status. This puts Clorox one step closer to our ambitious goal to reach ZWtL in 100% of our plants by 2025 and in our global facilities by 2030. We spoke with Wheeling senior engineer Jim Wood; plant health, safety and environment leader Zach Osiyemi; and plant manager Keith Toomey about how our teammates mobilized to make it happen.
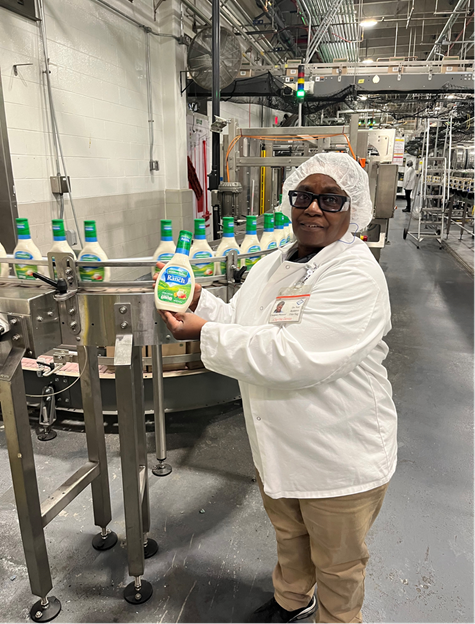
How did you engage and motivate your team to adapt to waste-reducing practices?
Meeting Clorox’s ZWtL criteria is no small feat, but the Wheeling team accepted the call to action, worked together to solve waste-flow hurdles and became our first Foods plant to achieve this goal. In recent years, the team adjusted their behaviors and implemented new processes throughout the plant to reduce, reuse and recycle waste. This includes simple operational shifts, like separation of waste streams and working with suppliers on reuse opportunities.
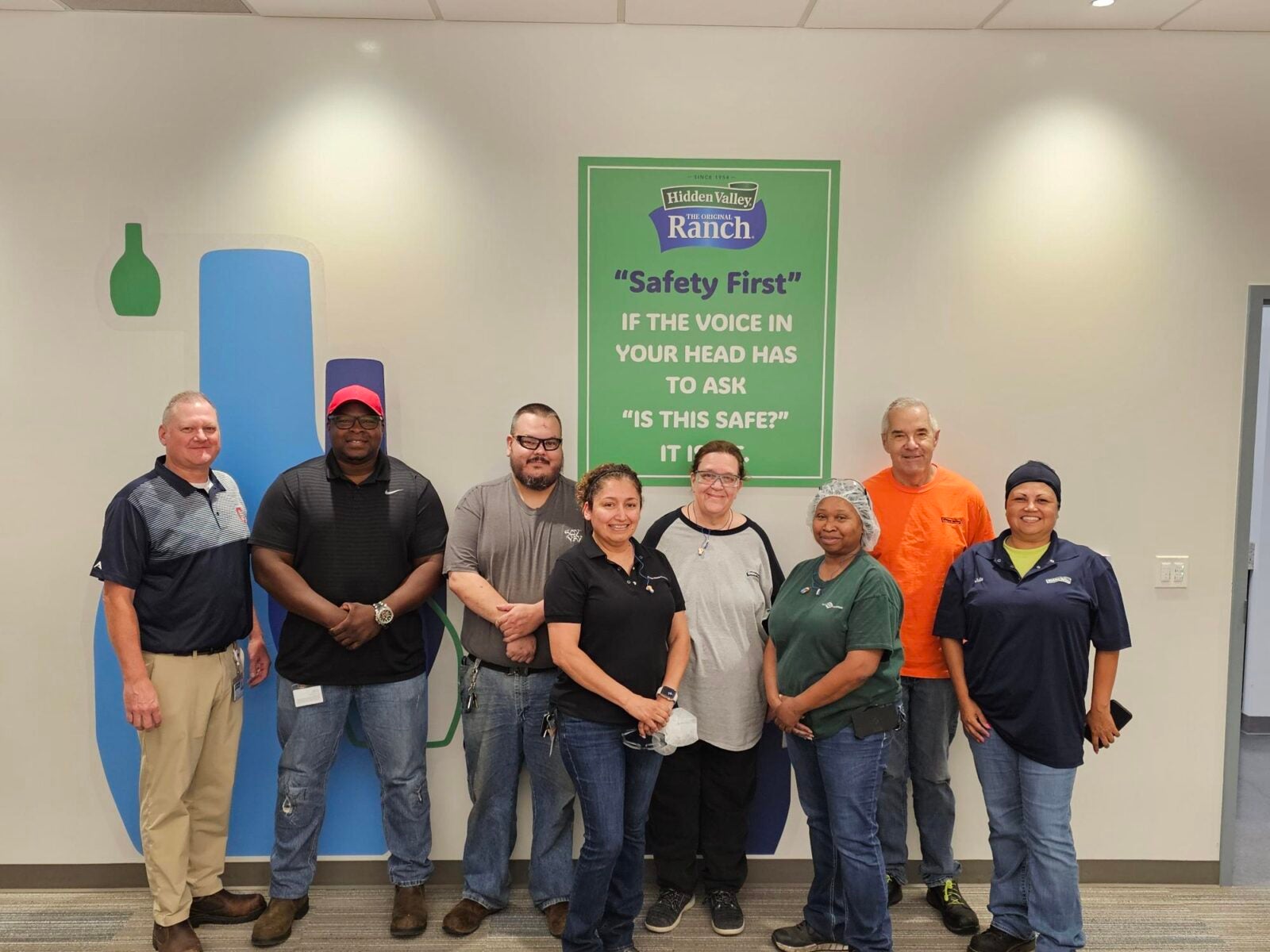
Were there any unique challenges this team faced during the transition to zero waste? How did they overcome them?
Food production presents unique challenges when it comes to reducing waste, so the Wheeling team had much to learn on this journey. Other Clorox locations are able to use waste-to-energy facilities to handle difficult-to-recycle materials, but the village of Wheeling does not have an operation in the area for this type of disposal. This compelled the team to research other ways of handling food-related waste streams; conduct trial runs to see if our product can be properly handled and discarded; then establish all new processes for storing, shipping and disposal that keeps scrap materials out of the local landfills.
The Wheeling team was persistent. Even when disposal outlets were identified, many options didn’t make logistical sense in terms of costs or air emissions associated with long-haul trucking of waste. The team wasn’t discouraged and ultimately unlocked new opportunities to reuse materials and significantly decrease the quantity of waste generated. Today, over 76% of the waste generated onsite is being reused in some way. For instance, the plastic pallets used to package and transport our bottles are sent back to our supplier for reuse.

What advice would you give to other manufacturing plants aiming to achieve zero waste?
This journey started with leadership — both at the plant and throughout the business. Having our leaders not only involved but leading the charge was critical to our success. When embarking on this challenge, it’s important to understand and be able to advocate for the “why” behind driving new processes that improve the business while also protecting the environment in the communities where we work and live.